
如何有效地选择和使用切削液?
洛斯润滑油 卓越品质/理想之选
切削液由于有冷却、润滑、清洗和防锈等功能,被广泛地应用在切削加工中。切削液在使用中经常出现变质发臭、腐蚀、产生泡沫、使用操作者皮肤过敏等问题,下面结合日常工作中的实际经验,谈谈切削液使用中的问题及其对策。
面对工厂的实际使用情况,如何有效地选择和使用切削液?
答:工厂现场的机器工作情况很复杂,影响切削液选用的因素很多,有时一些看起来不太重要的因素却成了决定切削液选用的关键。
例如插齿一般是粗加工,齿轮经插齿成形后尚需经剃齿工序进行精加工,选用活性较低的切削油既可满足工艺要求,又可获得较长的刀具寿命。这一般是指在齿轮加工车间而言,若此同一台插齿机是在一个修配车间里,齿轮加工的批量很小又无后续的剃齿工序,显然就应该选用高活性的切削油,因为此时产品的质量是主要因素,而刀具寿命及加工效率则是次要的。
所以切削液的选用因素及步骤不是固定的。但就一般情况而言,影响切削液选用有六大因素:
①加工工艺及相关条件(如加工方法、刀具及工件材料以 及加工参数等),这是最主要的;
②对加工产品的质量要求;
③职业安全卫生要求;
④废液处理要求和现场的条件;
⑤有关的法规方面的规定;
⑥使用经济性等。
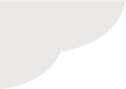
第一步:根据工艺条件及要求,初步判定是选用油基还是水基。一般来说,使用高速钢刀具进行低速切削时用油基,使用硬质合金刀具进行高速加工时用水基;对产品质量要求高、刀具复杂时用油基,主要希望提高加工效率时用水基;对于供液困难或切削液不易达到切削区时用油基(如内孔拉削、攻丝等),其他情况下尽量用水基。总起来说,用油基可获得较好的产品光洁度、较长的刀具寿命,但加工速度高时用油基会造成烟雾严重,只能用水基。
第二步:根据加工工艺选用油基或水基的同时还应考虑到有关消防的规定、车间的通风条件、废液处理方法及能力以及前后加工工序的切削液使用情况等。此外还应考虑工序间是否有清洗及防锈处理等措施。
根据上面两个步骤,确定油基或水基之后,再根据加工方法及条件、被加工材料以及对加工产品的质量要求选用具体品种。假设已选定用油基,再根据被加工材料的特性(如硬度、韧性等)、加工的参数(在此条件下是否易形成积屑瘤等)以及产品的光洁度要求来确定切削油的极压性和活性。最后再根据切削时的供液条件及冷却要求选用切削油的粘度。
在初步选定切削液后,还应从经济性的角度进行评价,从几种可能的方案中选出经济效果最好的切削液品种。
本文来源网络,仅供参考。感恩原创作者,版权归原作者所有,
如若侵权,烦请平台留言删除。
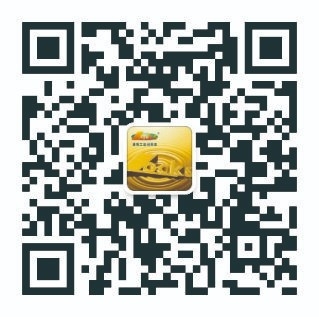
END